Salt mining. In the region
Salt - also known as white gold - brought Hall (Solbad Hall) great wealth back in the Middle Ages. Salt was mined around nine kilometers north of the town, in the so-called Halltal, until 1967. The salt works in Hall was first mentioned in a document in 1256. Salt mining therefore dates back at least to the Middle Ages.
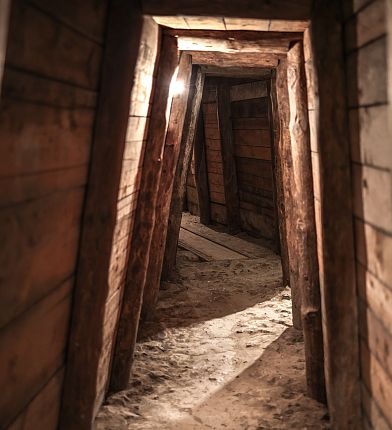
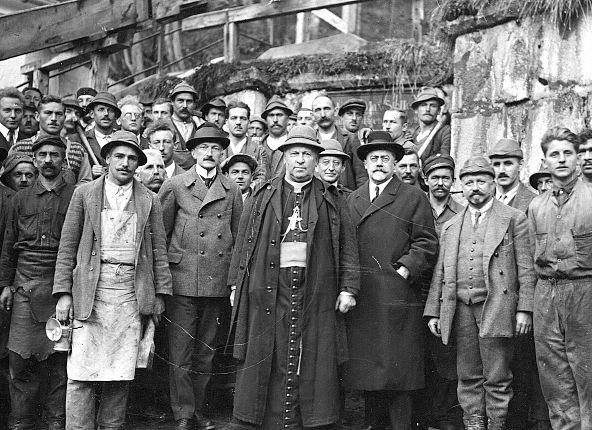
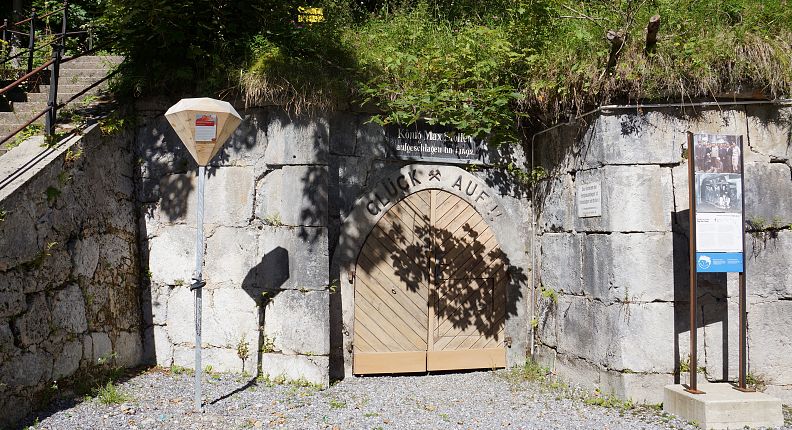
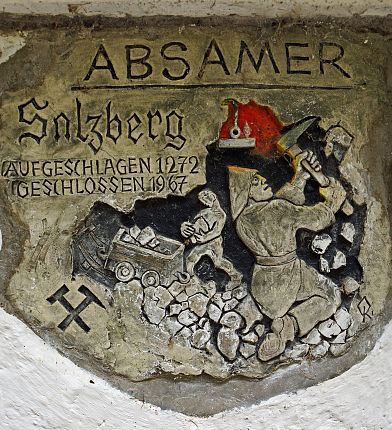
Location and formation of the salt mountain
The salt mountain, which has been opened up in eight horizons, lies at 1,334 to 1,635 meters above sea level. The extent of the still open, albeit no longer fully accessible, network is estimated at 20,000 meters, and together with the old structures at around 40,000 meters. Our alpine salt deposits belong to the Permian and Triassic formations and were formed around 200 to 300 million years ago (primordial sea or Tethys. As a result of the continental drift and the associated folding of the mountains, the plastic salt and clay masses of the primordial salt deposit, which lay at great depths, were pressed upwards through fissures and crevices into the mountain layers. This rock salt - a chemical compound of a metal (sodium) and a gas (chlorine) - is inextricably linked to the founding, naming, economic and social structure of the town of Hall, formerly known as Solbad Hall (1930-1974).
Discovery of the salt mountain in Halltal near Absam
A rich web of legends and stories surrounds the discovery of the salt mountain. One legend tells of a shepherd who extinguished his fire with spring water and discovered salt crusts on the charred remains of wood. Even better known is the tale of game or grazing cattle that tracked down the salty springs and drew the attention of hunters and shepherds to them.
Count von Brandis reports: "Anno Domini 1275, the magnificent Gotts Gab zu Haal was discovered in this way by Niclausen von Rohrbach, because he, as an avid hunter, had often been in the same mountains and observed that the deer and chamois, as well as the local cattle, were hiding in certain places and licking the salted stain, whereupon they began to dig, and the work was finally brought to its present, unimaginable state."
The fact that Count von Brandis dated the discovery of the salt mountain to 1275 is probably connected to the oldest official book of the Hall salt works. However, the significant salt sales around 1244, for example, speak against this year. The workers did not observe the required rest on Sundays and public holidays, whereupon Bishop Egno of Brixen gave the provost of Wilten the authority to order the workers at the salt works to observe the rest on public holidays by imposing church fines.
Liberation (jurisdiction)
In addition to many other rights, King Henry also granted the Pfannhaus the right of freedom, making it a courtroom independent of Hall's municipal court. The documentary evidence: "Whatever fornication and outrage happens in our Pfannhaus, as far as the eaves go, should be judged and corrected there and not elsewhere."
The enclosure of the Salzberg began at the mountain chapel in the Halltal valley, stretched up the valley and reached behind the Salzberg. Within this local free zone, no one employed at the Salzberg could be arrested by the Thaur district court. Outside of this area, every miner still had personal freedom, which was limited to minor offenses, if he was on his way from home to work on the Salzberg or back home from there.
Brine extraction on the Salzberg
Brine is extracted in salt mines. One hectoliter contains 32 kg of sodium chloride and secondary salts. The leaching process was also used at Wildanger in Halltal: The first cavity of a plant is blasted out at a diameter of 30 to 40 m and a height of 2 m (originally by hand). The plant cavity is always accessible from above via the invert chute, while it is closed off at the lower horizon with the plant box (sump).
The sump is filled with water up to the ceiling (factory roof), which dissolves the salt out of the hazel rock up to full saturation of 32 kg/hl. The insoluble components of the hazel rock (clay, gypsum, anhydrite) fall to the floor (factory floor) and form the factory brine. The brine produced is drained off through the plant box via the weir pipe inserted into the drainage dam. This process can be repeated continuously until the rock above the plant has been leached to the upper horizon
(final sky). Leaching takes place on the side walls of the plant and mainly on the roof of the plant, while a leaching stock builds up on the plant floor. As a result, the free plant space becomes larger and larger and moves from the bottom to the top and outside. In the very low-salt Haselgebirge mountains, the plant room fills up with laist and has to be cleaned in order to continue using it. Several plants with a capacity of up to 10,000 cubic meters were always in operation. The brine was fed into the salt works in Hall via a measuring trough, partly through wooden pipes and partly through cast iron pipes (from 1903).
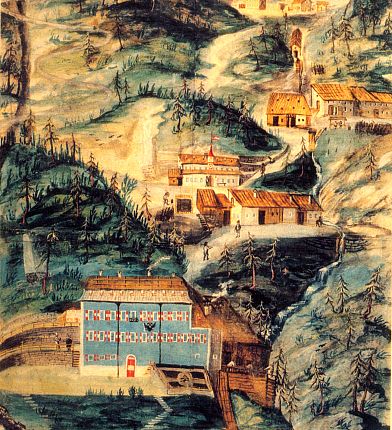
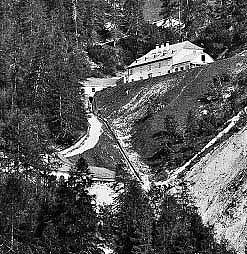
Salt extraction in the Hall salt works
Salt extraction or evaporation of the brine from the Halltal valley was last carried out (until 1951) in two coal-fired pans with a heating surface of around 140 m2 per pan. For centuries, the brewing pans were fired with wood that had been drifted from the Upper Inn Valley across the Inn to Hall. Hard coal from Bad Häring gradually replaced wood as an energy source. When the brine was evaporated with wood or coal, large quantities of water vapor escaped directly into the open air, which amounted to a huge loss of heat and therefore energy. In 1951, an ultra-modern thermo-compression plant was put into operation, which allowed a much more efficient method of operation (today's media tower). The "vapors" produced during the evaporation of the brine were compressed here by means of an electrically operated compressor, heated and fed back into the heating system of the evaporator. This made it possible to work more economically in a kind of cycle. However, the raw brine fed from the salt mountain into the brewhouse had to be cleaned beforehand to prevent the formation of scale in the evaporator.
In the brine purification process, secondary salts, e.g. magnesium compounds, were precipitated by adding milk of lime or calcium compounds (with the help of soda).
After purification, the brine was preheated and fed into the evaporator. The precipitated salt crystals collected in the lower part of the evaporator, from where they were pumped into the centrifuge in a pulpy state via a mixer. In the centrifuge, the moisture content of the salt was reduced to a residual level of around 2.5%. Conveyor belts transported the salt to the magazine, where it was prepared for dispatch by automatic packaging machines.